Aluminum alloys are based on aluminum and are produced ...
Aluminum alloys are based on aluminum and are produced by adding various elements such as manganese, magnesium, copper, silicon, iron, nickel, and zinc. It is relatively low in density and suitable for compressive strength, so it has gained more and more common use. According to different chemical composition and performance, aluminum alloys are divided into two types: formed aluminum alloys and CNC machined aluminum alloys.
Deformed aluminum alloys can be divided into aluminum alloys that are not strengthened by heat treatment processes and aluminum alloys that are strengthened by heat treatment processes according to their ability to strengthen their heat treatment processes. The functions of manganese, chromium and titanium in aluminum alloys are mainly to increase the plastic deformation temperature of the metal and weaken the commonality of its crystal growth. Nickel in aluminum alloys can improve the corrosion resistance and thermal strength of aluminum alloys. Fe, Si, Na, K, etc. all belong to the impurity elements in the aluminum alloy, among which are mainly Fe and St. Fe is not very soluble in aluminum, 0.5% at 655°C and only 0.002% at room temperature. Fe key produces the metallic compound FeAl3, which is a hard and brittle scaly chemical substance. The solubility of Si in aluminum is slightly greater, 1.65% can be incorporated at 577°C and 0.05% at room temperature. In addition to being integrated into the east and west of aluminum, Si appears independently in aluminum when it is unnecessary, which is usually called "dispersed silicon".
Due to the presence of many strengthening phases and overcapacity phases in aluminum
knurled insert, the as-cast structure exhibits multi-component doping. In addition, carbide mixtures are often present in as-cast structures of some aluminum alloys (eg, LY12). This material is usually hard and brittle, with a network of dislocations. In addition, due to the refrigeration standard during CNC machining, this chemical phase produces regional shrinkage porosity, cementite shrinkage porosity and intergranular segregation during casting. The plasticity of aluminum alloy casting is seriously reduced.
According to the thermoplastic deformation, the as-cast structure of the aluminum alloy can be greatly improved, and the characteristics can be greatly improved. Taking LY11 as an example, after extrusion deformation, a fiber structure is formed. Before the extrusion deformation level is lower than 70%, along with the improvement of the deformation level, the vertical and lateral hardness index values of the raw material are continuously improved. When the deformation level increases again, the vertical characteristics increase again, and the lateral characteristics drop sharply, which results in the heterosis resistance of the characteristics.
The division of streamline has great harm to the characteristics of aluminum alloy. Unsatisfactory streamline, eddy and flow through flow can significantly reduce the plasticity index value, fatigue limit and corrosion resistance of aluminum alloy. Therefore, when ordering the molding process, the streamlined position should be consistent with the higher bearing capacity of the part.
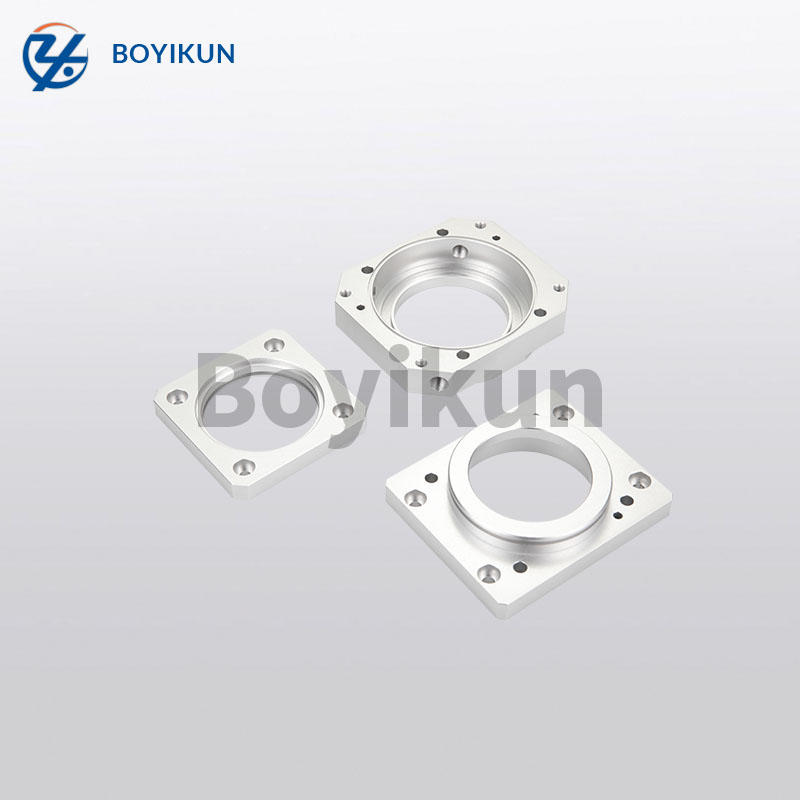