Cold forging is a process that creates finished parts from a variety of metals. The process requires less time and creates parts with a higher strength level than traditional methods. Some of the most common metals used for cold forging projects include hardened steel, stainless steel, copper, and aluminum.
Limitations of cold forging
Cold forging is an excellent choice for forming parts in high volumes, but there are some limitations to its use. The maximum deformation and shaping grade are much lower than those of hot forging. In addition, cold forged metals have less ductility, making them unsuitable for certain configurations. Additionally, residual stresses are possible due to the granular structure of the material. Finally, cold forging parts must undergo a heat treatment process to increase the ductility and strength.
Cold forging is generally not appropriate for parts with complex geometry. Consequently, it is used for smaller, lighter parts. However, it has some benefits, including high dimensional quality, excellent surface finish, and reduced material and weight. Experts in cold forging can help you make an informed decision regarding the type of cold forging process to use for your specific part design.
Cost-saving techniques
Cold forging is a cost-saving technique for metal parts. It is used to produce precision parts with tight tolerances and surface finishes that mirror the dies. In addition, the process is flexible and can produce parts with a broader range of material properties, shapes, and volumes. Moreover, cold forming is more cost-efficient than hot forging. It can reduce the cost of a part by up to 40% to 60%.
Cold forging involves a series of operations that move the material to the desired shape without working it. The temperature is kept at a level that is approximately 30% below the recrystallization temperature of the metal. The workpiece is then inserted into a die and shaped by squeezing, pressing, or drop forging hammers. These processes can achieve complex shapes in a short period of time. In addition, cold forging improves the mechanical properties of metal and increases its overall strength. It is also less prone to fatigue failure.
Dimensional accuracy
Forging processes are subject to several errors, including the dimensional accuracy of the forged part. The difference between the forged part and the die dimension is due to the thermal effect and elastic deformation of the die, and the amounts vary according to the forging conditions. Dimensional accuracy of cold forged parts can be improved by using FEA (Finite Element Analysis) to simulate the forging process and predict the required die dimension. The accuracy of the FE simulation depends on the number of variables, such as the material model used to calculate the forged part. Other considerations that can enhance dimensional accuracy include the ejecting and loading stages.
Dimensional accuracy is a crucial factor for the success of a cold forged part. The high precision of cold forged parts helps manufacturers reduce manufacturing costs and increase production quantities. Cold forged parts are often produced to JIS class 3-4 precision, which is a significant advantage over other metal products. The process of cold forming also allows for shorter production cycles, enabling manufacturers to produce large volumes of forged products quickly.
Design freedom
Cold forged parts can handle high stress and can be produced to exacting tolerances. This process also allows for the creation of intricate shapes and contours. It also offers design freedom, which makes it a great choice for parts with complex geometry. In addition, cold forged parts are lightweight and durable.
Cold forged parts can be produced on a vertical press or cold forming machine. Each section of the machine performs a specific operation. The machines range from single-die to multiple-die forming. They are most effective for large-volume production. Cold forged parts can be a variety of shapes, including long and thin sections. Cold forged parts can incorporate any design element, from simple shapes to complex curves.
Customized designs
Cold forging is a process of transforming bar stock into metal shapes using localized compressive force. It is a highly efficient and cost-effective way of producing parts with high strength and tight tolerances. In addition, the cold-forming process eliminates the need for cutting during gear shaping. It also allows for the production of parts at high production rates and high volumes.
Cold forging is an efficient method for producing parts with high strength, due to the fact that the material is not overheated. In addition, it provides superior mechanical properties and minimizes the risk of casting defects. It is a cost-efficient process that is suited for complex shapes and high-volume manufacturing.
cold forged part
Location:China
Business Type:Manufacturer, Exporter
Certificate:ISo 9001:2015 IATF 16949:2016
Terms of payment and delivery:100% T/T in advance for samples, can negotiate for bulk order. ex-work forsamples, FOB Ningbo for bulk order, or customers' forwarder.
Price:Consultation
Packing details:In platic bags inside carton, blister packing in case of damage for special parts.accordint to customers' requirements
Delivery time:1-3weeks for samples, confirm the delivery date after sample approval
Payment method:T/T ( prefer this ). L/C.D/P at sight , Paypal
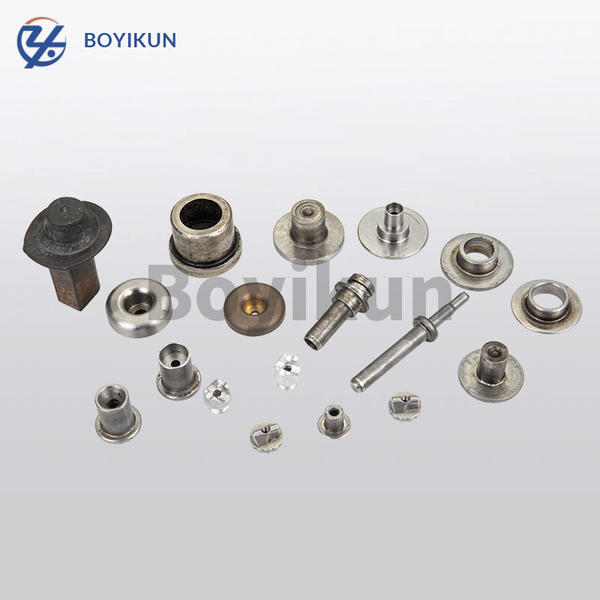