Abstract:When it comes to CNC machining, time is money. For low-volum...
When it comes to CNC machining, time is money. For low-volume production, part setup, programming, and machine running time often far exceed material costs.
Understanding how the geometry of the part determines the machine tool required is an important part of minimizing the number of settings a mechanic needs to perform and the time it takes to cut the
aluminum bushing. This can speed up the part manufacturing process and save you costs.
1. Create a wide corner radius
The end mill will automatically leave a rounded inner corner. A larger corner radius means that larger tools can be used to cut the corners, which reduces running time and therefore costs. In contrast, a narrow inner corner radius requires both a small tool to machine the material and more passes—usually at a slower speed to reduce the risk of deflection and tool breakage.
In order to optimize the design, please always use the largest corner radius possible and set the 1/16” radius as the lower limit. A corner radius smaller than this value requires very small tools, and the running time increases exponentially. In addition, if possible, try to keep the inner corner radius the same. This helps eliminate tool changes, which increase complexity and significantly increase runtime.
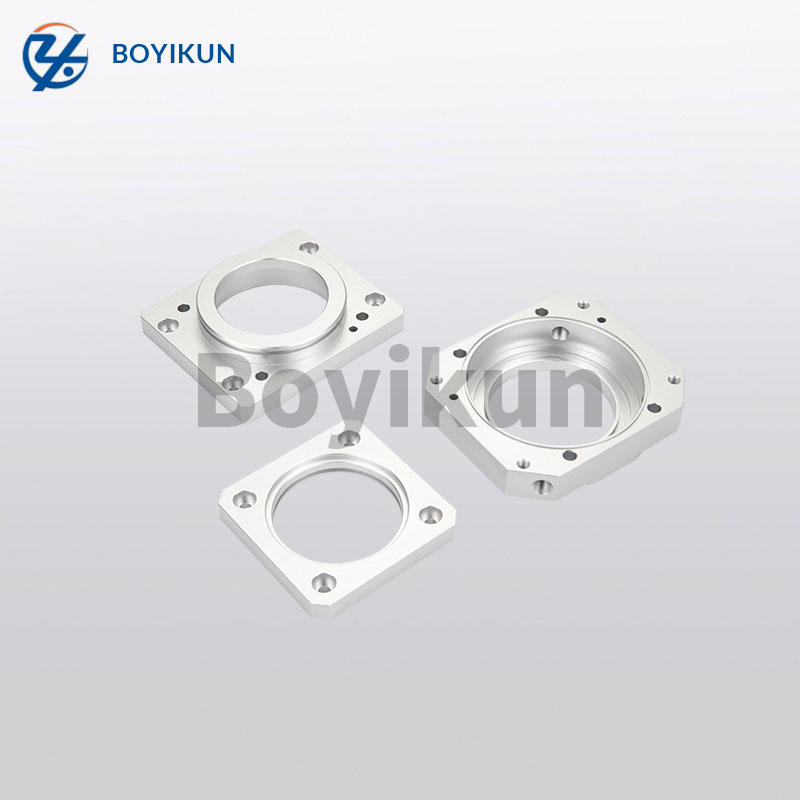
2. Avoid deep pockets
Parts with deep cavities are usually time-consuming and costly to manufacture. The reason is that these designs require fragile tools, which are prone to breakage during machining. To avoid this situation, the end mill should gradually "decelerate" in uniform increments. For example, if you have a groove with a depth of 1”, you can repeat a pass of 1/8” pin depth, and then perform a finishing pass with a cutting depth of 0.010” for the last time.
3. Use standard drill bit and tap size
Using standard tap and drill bit sizes will help reduce time and save part costs. When drilling, keep the size as a standard fraction or letter. If you are not familiar with the size of drill bits and end mills, you can safely assume that traditional fractions of an inch (such as 1/8", 1/4" or millimeter integers) are "standard". Avoid using measurements such as 0.492" or 3.841 mm. For taps, 4-40 taps are more common and usually more usable than 3-48 taps.