Aluminum alloy steel castings refer to product workpiec...
Aluminum alloy steel castings refer to product workpieces or vacancies obtained by CNC machining and deformation of metal material blanks. Using the working pressure on the metal material blank to shape and deform it can change its physical properties. Steel castings can be divided into cold forging temperature steel castings and hot parts according to the processing temperature of the blank. Cold steel castings are generally processed at room temperature, and hot steel castings are processed at a temperature higher than the plastic deformation temperature of the metal material blank.
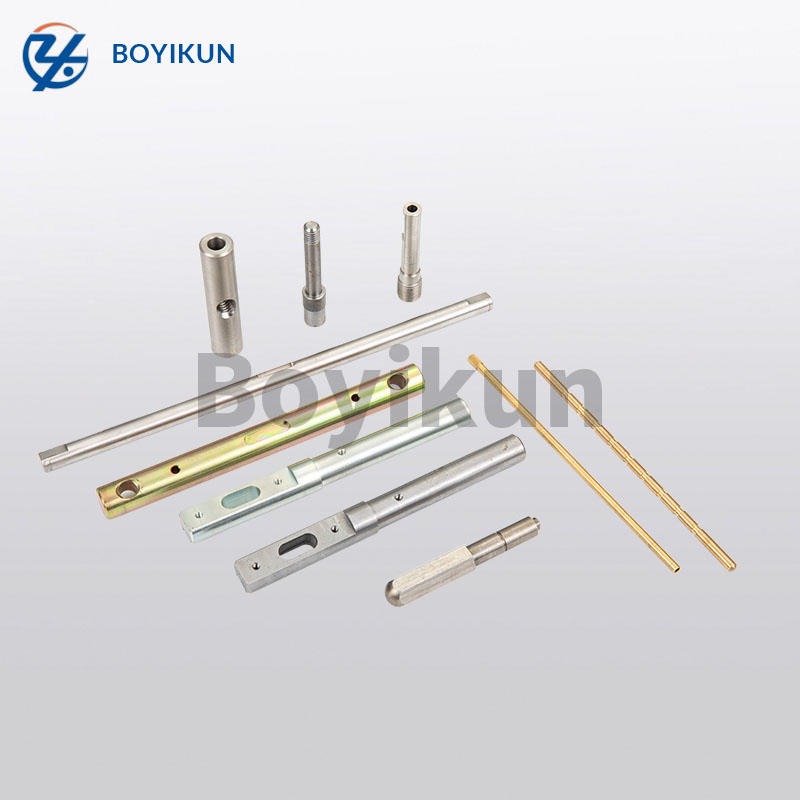
1. Aluminum alloy has small capacity, high precision, high diversity, small processing capacity or partial processing after forging, or even no processing;
2. The chemical fiber of aluminum alloy steel castings is continuous, the physical properties are good, and the variety is not significant. Due to the large deformation of the forging blank in the isothermal process, the fluidity of the metal material is uniform, and the equiaxed fine-grain structure can be obtained for the steel casting, which significantly enhances the tensile strength, low cycle fatigue characteristics and internal stress corrosion resistance of the casting;
3. Aluminum alloy steel castings have no residual stress. Because the vacancy plastic deformation strain rate is super slow at high temperature, the metal material is completely softened, the internal structure is well-proportioned, the internal and external internal stress is different during the basic CNC machining process, the residual deformation is removed, and the specifications are stable after the heat treatment process;
4. High utilization rate of raw materials. During basic CNC machining, the utilization rate of raw materials for steel castings is increased to 60%-90%, and the utilization rate is increased to 60%-90% due to the selection;
5. Improve the plasticity of metal materials. Because in the case of slow deformation in the isothermal process, the dislocations in the deformed metal material have time to respond and can be dynamically plastically deformed, so that the deformed metal material has better plasticity.