When to choose CNC machining instead of casting
If you start with die casting, why choose to redesign your parts and use CNC machining instead? Although casting is more cost-effective for high-volume parts, CNC machining is the best choice for low to medium-volume parts.
CNC machining can better meet the tight delivery cycle, because there is no need to make molds, time or costs in advance during the machining process. In addition, in any case, die casting usually requires machining as an auxiliary operation. Post-processing is used to achieve certain surface finishes, drilling and tapping holes, and to meet the strict tolerances of cast parts that are matched with other parts in the assembly. And post-processing requires custom fixtures, which in itself is very complicated.
CNC machining can also produce higher quality parts. You can be more confident that each part will be manufactured consistently within your tolerance requirements. CNC machining is naturally a more precise manufacturing process, and there is no risk of defects in the casting process, such as pores, dents, and improper filling.
In addition, casting complex geometries requires more complex molds, as well as additional components such as cores, sliders or inserts. All these add up, and even before the start of production, a lot of money was invested in cost and time. Not only complex parts are more meaningful for CNC machining. For example, CNC machine tools can easily manufacture flat plates by processing stock materials to the required size and thickness. However, casting the same metal plate can easily cause filling, warping or sinking problems.
How to transform casting design into CNC machining design
If you decide to redesign the part to make it more suitable for CNC machining, you will need to make several key adjustments. You must consider the draft angle, groove and cavity, wall thickness, critical dimensions and tolerances, and material selection.
Remove the draft angle
If you initially considered casting when designing the part, it should include the draft angle. As with injection molding, the draft angle is very important so that the part can be removed from the mold after it has cooled. When machining, the draft angle is unnecessary and should be removed. Designs that include draft angles require a ball-end milling cutter to process and increase your overall processing time. The extra machine time, extra tools and extra tool change operations mean extra costs-so save some money and give up the draft angle design!
Avoid large and deep grooves and hollow cavities
In casting, shrinkage holes and hollow cavities are usually avoided, because thicker areas are often not filled well and may lead to defects such as dents. These same functions take a long time to process, and doing so will produce a lot of wasted material. Moreover, since all the forces are on one side, once the part is released from the fixture, the stress of the deep cavity can cause warpage. If grooves are not a critical design feature, and if you can afford the extra weight, consider filling them, or adding ribs or gussets to prevent warping or deformation.
The thicker the wall, the appointment
Likewise, you need to consider the wall thickness. The recommended wall thickness for castings depends on the structure, function, and material, but is usually relatively thin, ranging from 0.0787-0.138 inches (2.0-3.5 mm). For very small parts, the wall thickness can be even smaller, but the casting process needs to be fine-tuned. On the other hand, CNC machining has no upper limit on wall thickness. In fact, thicker is usually better, because it means less processing and less material waste. In addition, you can avoid any warping or deflection risks that may occur in thin-walled parts during processing.
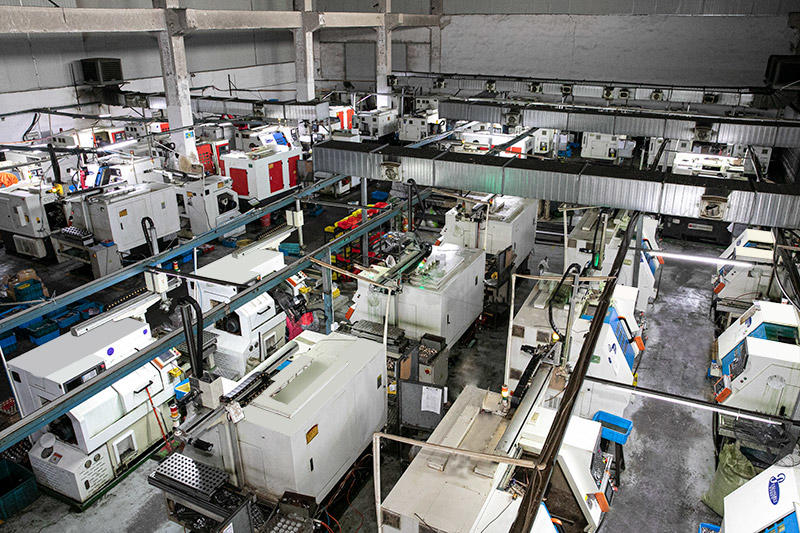
Tight tolerance
Casting usually cannot maintain tight tolerances like CNC machining, so you may have made concessions or compromises in the casting design. With CNC machining, you can fully realize your design intent and make more precise parts by eliminating these compromises and implementing tighter tolerances.
Consider using a wider range of materials
Last but not least, CNC machining provides a wider choice of materials compared to casting. Aluminum is a very common die casting material. Zinc and magnesium are also commonly used in die casting. Other metals, such as brass, copper, and lead, require more special processing to produce high-quality parts. Carbon steel, alloy steel and stainless steel are rarely die cast because they are prone to rust.
On the other hand, in CNC machining, there are more metals suitable for machining. You can even try to make your
stainless steel turned parts out of plastic, because there are many plastics that can be processed well and have useful material properties.
in conclusion
Although casting is a great process in some cases, CNC machining is sometimes more suitable for the function or manufacturing needs of the part. If this is the case, make sure to redesign your parts to achieve the most efficient and economical CNC machining process.